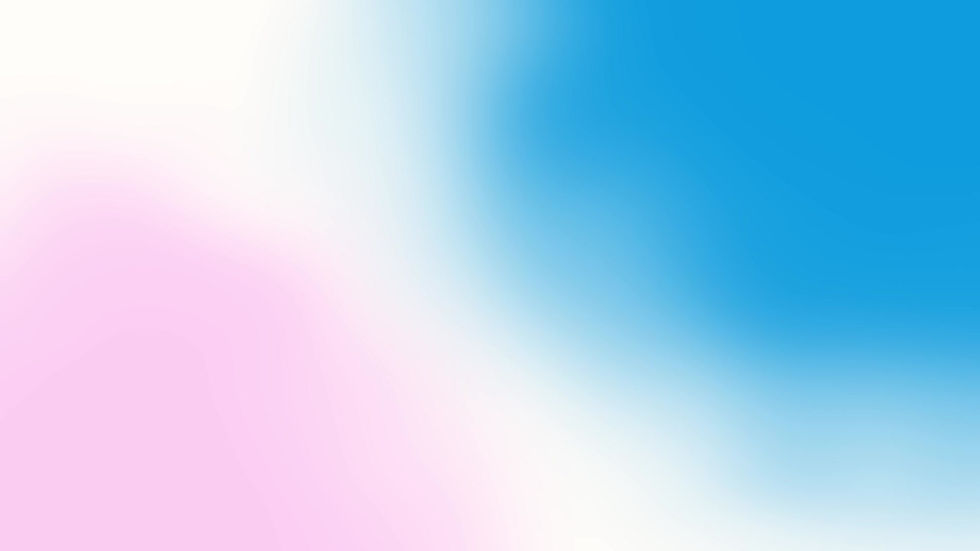
Our Services
At Mediscient Devices, we offer innovative medical injectors and a range of services that includes benchmarking, product design, process development, assembly machines, and production. Our team of experts is dedicated to providing you with a seamless experience and ensuring the success of your medical equipment manufacturing projects.
Benchmarking
Design
Prototyping
Process Design
Mold Development
Assembly Machine Development
Product Development
Production Line
Development
Technical Documentation
& Product Filing
Commercial
Supply
Product & Process Validations
Product Development
-
User step analysis
-
Force testing at each and every step
-
21CFR compliant testing equipment
-
With audit trail reporting
-
-
Material Identification tests in associated labs
-
FTIR
-
DSC
-
Residue
-
-
Patent Study
-
Inhouse study
-
Patent attorney associate
-
-
Mechanism study:
-
Measuring every dimension of all component parts
-
Measuring forces of every functional feature of all component parts
-
Identifying part manufacturability details like parting lines, gate points, ejection points, etc.
-
Hot tip cutters, surgical cutters, handheld motorized micro cutter for opening up the devices/ cutting sections
-
Reverse Engineering with NABL calibrated equipment
-
1micron LC camera Vision Measurement Machine (VMM)
-
21 CFR Universal Testing Machine (UTM)
-
Different Force gauges
-
Vernier calipers, Micrometers, height gauge, surface plate, runout dial gauge and stylus, etc.
-
Custom gauges
-
-
3d model generation
-
Part modeling
-
Generating parting lines
-
Creating gate points and ejection points
-
Component assembly
-
Rendering
-
-
Production Line Development
-
Define process requirements
-
Assembly sequencing
-
Define assembly requirements
-
Define, Assembly Concept
-
Define SPM/equipment for assembly
-
Molding process design and development
-
Validation protocols development (IQ, OQ, PQ)
-
Define tool certification/validation requirements and ensuring all relevant data.
-
Define Scientific Mold Validation Protocol
-
Define product approval criteria, batch release criteria
-
Define product testing protocols (3rd party lab)
-
Listing Product certification requirements
Product Filing & Commercial Supply
-
Design History File (DHF)
-
User Needs (URS)​
-
Design Input
-
Design Output
-
Design Verification
-
Bench testing
-
Design Validation
-
DV & DVL testing
-
-
Risk Management File
-
Risk Management Plan (RMP)
-
Hazard Assessment (IHA)​
-
Different types of Failure Mode Analysis
-
Benefit Risk
-
Risk Summary
-
-
US DMF filing
-
Device History File
